Understanding Diluent in the Oil and Gas Industry
1. Introduction
In the oil and gas industry, a diluent is a light hydrocarbon fluid used to reduce the viscosity of heavy crude oil or bitumen, facilitating its transportation through pipelines. Heavy crude oils are naturally dense and viscous, making them challenging to transport efficiently. By blending these heavy oils with diluents, their flow characteristics are improved, enabling smoother and more cost-effective movement from extraction sites to refineries. Crude oil is typically transported from production sites to refineries via pipelines. However, for heavy crude oils with an API gravity below 15°, this process requires specialized infrastructure. The primary challenge with these heavy crudes is their extremely high viscosity, which can range from a few thousand to several million centipoises at reservoir temperature. Since pipeline transport generally requires a maximum viscosity of around 400 cP, the most effective solution currently available is the addition of a diluent to reduce viscosity. While alternative methods such as oil-in-water emulsions and core annular flow show potential for future applications, diluent blending remains the industry standard for ensuring the smooth flow of heavy crude through pipelines (P. Gateau, 2004).
2. Importance of Diluent in Transporting Heavy Crude Oil
Heavy crude oils and bitumen are characterized by their high density and viscosity, making them challenging to transport efficiently. Without dilution, these substances do not flow easily, posing significant difficulties for pipeline transportation. By blending heavy crude with diluents, the mixture’s viscosity is reduced, allowing it to meet pipeline specifications and flow more readily. This process is essential for moving heavy crude from production sites to refineries and markets.
Transportation of crude oil requires robust systems tailored to the volume, topography, and distance. Each of the several strategies utilised to make sure that the transportation of crude oil satisfies the high demand has advantages and disadvantages (Dombor, 2025).
The detail of the transport methods is mentioned in the table below.
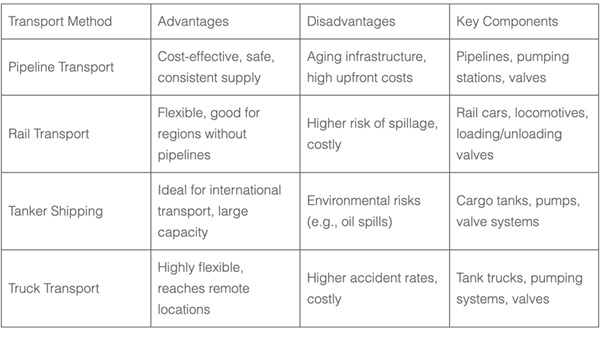
3. Role of Diluent in Reducing Viscosity and Enabling Pipeline Transport
Heavy crude oil and bitumen have extremely high viscosity, making them difficult to transport through pipelines. Diluent plays a critical role in reducing this viscosity by acting as a thinning agent, ensuring the oil meets pipeline transport requirements. When mixed with heavy crude, diluent decreases the internal resistance to flow, making it more manageable for pumps and pipeline systems. Without dilution, the transport of such high-viscosity crude would require excessive energy, leading to higher operational costs and potential damage to infrastructure.
Recent research has explored innovative sources for diluent. Thermal cracking tests have been conducted to obtain hydrocarbon condensates from common plastic waste, such as postconsumer low-density polyethylene (LDPE) plastic bags. These hydrocarbons, due to their chemical similarity to traditional diluents, have been successfully used to dilute heavy crude oil (12°API), resulting in a 90% viscosity reduction at room temperature for a 5:25 vol:vol blend of hydrocarbons and heavy crude oil. This approach not only enhances crude oil transport efficiency but also offers a sustainable solution for plastic waste recovery. However, large-scale industrial implementation would require integration with municipal solid waste collection and pre-treatment technologies to ensure a steady supply of suitable hydrocarbon feedstock (Cuauhtémoc Pozos Vázquez, 2019).
3.1. Diluent Blending with Crude Oil Before Transportation
The blending of diluent with crude oil typically occurs at the production site or upstream processing facilities. Producers add a calculated proportion of diluent, which can range from 15% to 50%, depending on the crude’s viscosity, the type of diluent used, and the transportation requirements. The mixture, commonly known as dilbit (diluted bitumen) or synbit (a blend with synthetic crude), is then transported via pipelines to refineries. Once at the refinery, the diluent is often recovered and recycled for reuse in future blending operations.
With emerging research highlighting alternative diluents from recycled plastic waste, the industry could move toward a more sustainable and cost-effective method of reducing crude oil viscosity while addressing environmental challenges related to plastic disposal (Choksi, 2024).
3.2. Different Blending Methods for Heavy Crude Oil Transport
The methods used for blending diluents with heavy crude oil can be categorized into conventional and emerging techniques. These include:
- Dilution Method: The most common technique, where lighter hydrocarbons like condensate, naphtha, or kerosene are mixed with heavy crude to reduce viscosity.
- Advantages: Simple, widely used, cost-effective.
- Disadvantages: Requires continuous supply of diluent, increases operational costs.
- Emulsification: Water or surfactants are used to create stable oil-in-water emulsions for easier transport.
- Advantages: Reduces viscosity effectively, can use low-cost water.
- Disadvantages: Emulsions require chemical additives and separation processes.
- Friction Reduction: Special additives are introduced to minimize resistance during pipeline flow.
- Advantages: Enhances pipeline efficiency, reduces pumping costs.
- Disadvantages: Requires precise dosing; some agents degrade over time.
- Annular and Core Flow: A method where the heavy crude flows at the centre of the pipeline while surrounded by a low-viscosity fluid, reducing drag.
- Advantages: Minimizes pipeline drag, reduces energy consumption.
- Disadvantages: Complex setup, requires additional infrastructure.
- Thermal and Electrical Heating: Direct heating or electrical induction lowers viscosity by increasing temperature.
- Advantages: Immediate viscosity reduction, effective for short distances.
- Disadvantages: High energy consumption, not suitable for long pipelines.
- Ultrasonic and Microwave Treatment: High-frequency waves break down large hydrocarbon molecules, making the crude less viscous.
- Advantages: No need for chemical additives, effective in viscosity reduction.
- Disadvantages: High initial cost, requires specialized equipment.
- Solar Heating: Using solar energy to preheat crude before transport.
- Advantages: Environmentally friendly, reduces operational costs.
- Disadvantages: Weather-dependent, limited scalability.
- Electromagnetic Field Conditioning: Altering the molecular structure of crude oil using electromagnetic waves to improve flow.
- Advantages: Non-contact method, effective for specific crude types.
- Disadvantages: Expensive setup, effectiveness varies with crude composition.
- Thermochemical Heat Treatment: Chemical reactions generate heat within the crude oil, reducing viscosity.
- Advantages: Can be applied in remote areas without external energy sources.
- Disadvantages: Requires careful handling of chemicals, potential environmental impact.
- Plasma Heating: High-energy plasma is applied to modify the properties of heavy crude for better pipeline transport.
- Advantages: Rapid heating, potential for improved oil recovery.
- Disadvantages: High energy consumption, expensive equipment.
Each method has its own trade-offs, and the choice depends on cost, infrastructure, and crude oil characteristics (Rakesh Kumar Ratnakar a, 2024).
4. Types of Diluent Used in the Industry
1. Natural Gas Condensate
- Description: Light hydrocarbon liquids extracted from natural gas fields, composed mainly of pentanes and heavier hydrocarbons.
- Advantages: Readily available in gas-producing regions, effectively reduces crude viscosity.
- Disadvantages: Can vary in composition, requiring adjustments in blending.
2. Naphtha
- Description: A petroleum-derived liquid hydrocarbon used as a blending agent in crude oil transportation.
- Advantages: Compatible with refining processes, commonly used in oil sands production.
- Disadvantages: More expensive than natural gas condensate, requires careful handling due to volatility.
3. Synthetic Crude Oil (SCO)
- Description: An upgraded product from bitumen or heavy oil, used as a diluent.
- Advantages: Has refining value, reduces the need for external diluents.
- Disadvantages: Energy-intensive to produce, limited availability.
4. Other Blending Agents
- Description: Includes light crude oils, refinery streams, and alternative diluents like bio-based solvents.
- Advantages: Provides flexibility in blending based on availability and crude properties.
- Disadvantages: Blending consistency varies, and some agents may require additional processing.
Each diluent has specific properties that impact blending efficiency, cost, and overall transportability of heavy crude (cer-rec, 2022).
5. Factors Affecting Crude Oil Viscosity and Techniques to Reduce it
5.1. Factors Affecting Crude Oil Viscosity
- API Gravity: Lower API gravity indicates heavier crude, which has higher viscosity and requires more dilution.
- Temperature: Viscosity decreases with increasing temperature, making heating a viable option for transport.
- Composition: The presence of heavy hydrocarbons, asphaltenes, and waxes increases crude oil viscosity.
- Water and Impurities: Emulsified water and impurities can alter viscosity and affect flow characteristics.
5.2. Techniques to Reduce Viscosity
- Dilution with Diluents: Blending heavy crude with light hydrocarbons (natural gas condensate, naphtha, synthetic crude) to improve flow.
- Heating: Raising the temperature to reduce viscosity, often used in conjunction with insulated pipelines.
- Emulsification: Mixing crude oil with water and surfactants to form oil-in-water emulsions with lower viscosity.
- Drag-Reducing Agents (DRA): Chemical additives that reduce pipeline friction and enhance flow.
- Core Annular Flow: Transporting heavy crude as the core within a surrounding layer of water to reduce friction.
- Ultrasonic and Microwave Treatment: Breaking down heavy hydrocarbons at a molecular level to improve fluidity.
- Electromagnetic and Plasma Heating: Using advanced technologies to modify crude properties and lower viscosity.
6. Influence of Composition on Crude Oil Viscosity
Crude oil can be categorized into non-colloidal liquids, maltenes, and asphaltenes. Asphaltenes are dark brown powders that can clump together, significantly increasing oil viscosity. Studies by various authors have explored the impact of asphaltene concentration on heavy crude viscosity.
Hénaut (2001) found that adding asphaltenes (0–20% by mass) to maltenes increased viscosity dramatically. For instance, maltenes had a viscosity of 20,000 cP, while a sample with 17% asphaltenes reached 600,000 cP. All samples behaved as Newtonian fluids, with viscosity rising as asphaltene concentration increased.
Argiller et al. (2002) observed that above a critical asphaltene concentration (10% by weight), mixtures of maltenes and asphaltenes not only became much more viscous but also exhibited stronger elastic properties.
Ghanavati et al. (2013) studied dehydrated heavy oil, extracting asphaltenes to create maltene samples. They added varying asphaltene concentrations and found that viscosity increased linearly at low concentrations but rose sharply at higher levels due to stronger particle interactions. Temperature had a more significant effect in high-concentration regions.
Luo and Gu (2005) confirmed these findings, showing that reconstituted heavy oil with 14.5% asphaltenes had a viscosity of 23,199 cP at 23.9°C, compared to only 767 cP for maltenes. They concluded that asphaltenes are the primary cause of high viscosity in heavy oil, especially when they flocculate (Oliveira, 2017).
7. Detailed Review on the Methods for reducing crude oil viscosity
Traditionally, heavy and extra-heavy crude oils have had limited demand due to their high viscosity and complex composition, making extraction, transportation, and refining both challenging and costly. Addressing these issues requires advanced technological solutions. Various methods have been explored to reduce the viscosity of these crudes and enhance their flow through pipelines. These include blending with light oils or alcohols, heating production lines or the crude itself, using emulsion-based viscosity reducers, and incorporating viscosity-reducing additives in aqueous surfactant solutions (Azodi & Nazar, 2013; Sanchez & Zakin, 1994). The following section reviews the current status of these techniques (Santos, 2017)
7.1. Dilution of crude oil with light oils or alcohols
Dilution is one of the oldest and most effective methods for reducing the viscosity of heavy crude oil. This technique involves blending heavy crude with lighter hydrocarbons or solvents, such as light oil or alcohol, to improve its flow properties and facilitate transportation through pipelines. Typically, adding 20–30% solvent is sufficient to avoid high-pressure drops or the need for elevated temperatures. Additionally, dilution can aid in the dehydration and desalination of heavy crude. However, this method requires significant investment in pumping and pipeline infrastructure, as well as processes to separate the solvent from the crude oil at the destination.
Studies have demonstrated the effectiveness of dilution. For example, Yaghi and Al-Bemani (2002) found that mixing heavy and light oils in a 7:3 ratio reduced viscosity from 15,000 cP at 20°C to 1,000 cP at 30°C and 300 cP at 50°C. Hasan et al. (2010) explored the use of alcohol and light oil as diluents. Adding 10% alcohol reduced viscosity from 10,000 cP to 2,000 cP, while 20% alcohol lowered it to 9,500 cP. Alcohol interacts with asphaltenes, breaking down their structure and reducing viscosity. Similarly, mixing heavy crude with 10% light oil reduced viscosity to 1,200 cP, and 20% light oil brought it down to 350 cP, which is 26 times lower than the original viscosity. These results highlight the effectiveness of light oil as a diluent compared to alcohol.
Other solvents, such as dimethyl ether (DME) and pentan-1-ol, have also been studied. DME is advantageous because it is easier to recover at refineries compared to other solvents. Pentan-1-ol, a type of alcohol, is more effective than kerosene in reducing viscosity due to its hydrogen bonding with asphaltenes. However, solvents with high polarity or strong hydrogen bonding can themselves be viscous, limiting their effectiveness. Only polar solvents with minimal hydrogen bonds significantly reduce crude oil viscosity.
Despite its benefits, the dilution method faces challenges. Changes in oil composition can alter the required oil-to-solvent ratio, and the use of solvents like naphtha or light oil can destabilize asphaltenes, causing them to flocculate and precipitate. This can lead to pipeline blockages and other operational issues. Furthermore, the economic viability of dilution depends on the cost of the light fractions used as solvents, which may not always be offset by the increased value of the treated heavy oil. Careful economic and technical analysis is necessary to ensure the feasibility of this method. Overall, while dilution is a proven and widely used technique, further research is needed to optimize its application and address its limitations (Mansur, 2017).
7.2. Heating of production lines or the crude oil
Heating is the second most widely used method to reduce the viscosity of heavy oils for pipeline transportation. The principle behind this technique is that viscosity decreases as temperature rises, making the oil easier to pump. To achieve this, the oil must be heated to a temperature where its viscosity is significantly reduced. Maintaining this high temperature is crucial, which is often done by insulating pipelines to preserve heat. For instance, burying pipelines can help retain heat, but external heating is usually necessary due to heat losses caused by slow oil flow. Reheating is typically done at pumping stations using direct heaters. Additionally, traditional pipelines can operate at low vapor pressure, close to environmental pressure, to maximize their capacity.
However, heating production lines has its drawbacks, particularly for long-distance or offshore operations. The high costs associated with maintaining elevated temperatures over long distances are a significant challenge. Offshore operations face additional difficulties due to the cooling effect of seawater and the complexity of installing and maintaining submerged pumping and heating stations. These factors make heating a less economical option in certain scenarios, despite its effectiveness in reducing viscosity (Mansor, 2017).
7.3. Mixtures with chemical viscosity reducing additives
Xie et al. (2001) studied the effects of oil-based and water-based chemical additives on crude oil viscosity. They found that oil-based additives were effective for reducing the viscosity of low- to medium-viscosity crude oils, while water-based additives worked particularly well for high-viscosity crude oils. Chemical additives have been widely researched for their ability to enhance heavy crude oil recovery, but their effectiveness is highly selective and depends on the specific composition of the crude oil. For example, heavy oils from Mexico often contain high levels of asphaltenes (> 8% by weight), low paraffin content, and significant amounts of sulfur (> 1.9% by weight), nickel, and vanadium, which influence the choice of additives.
Castro et al. (2011) investigated the impact of thermopolymers—made from styrene (S), n-butyl acrylate (BuA), and vinyl acetate (VA)—on the viscosity of heavy oil from the Gulf of Mexico. The oil had an API density of 15.82, 19.92% asphaltenes, and a kinematic viscosity of 2984.97 mm²/s at 25°C. The thermopolymers, prepared at 20% concentration in toluene and applied at 1000 ppm, reduced the oil’s apparent viscosity. The efficiency of these polymers depended on their molecular structure and affinity with the oil’s components (saturates, resins, asphaltenes, and aromatics). Polymers rich in styrene (S) were the most effective, as the aromatic nature of styrene allowed strong interactions with asphaltenes and resins. Vinyl acetate (VA) added polarity, enhancing interactions with resins, while n-butyl acrylate (BuA) promoted interactions with paraffins. The study also found that polymers with similar compositions but different molecular masses had comparable viscosity-reducing effects, especially at shear rates above 2 s⁻¹.
In another study, Junaki et al. (2012) developed an ionic additive called IRAN91 and tested it on heavy oil samples from the Marun oil field in Iran. They observed that this additive reduced the viscosity of heavy oil by up to 64%, demonstrating its potential as an effective flow enhancer. These findings highlight the importance of understanding crude oil composition and the chemical structure of additives to optimize viscosity reduction in heavy oils (Oliveria, 2017).
7.4. Formation of heavy crude oil emulsions in water (O/W)
Oil-in-water (O/W) emulsions are an effective method for reducing the viscosity of heavy crude oils, making them easier to transport through pipelines. These emulsions consist of oil droplets dispersed in a continuous water phase, with the viscosity of the emulsion being significantly lower than that of the original crude oil. This method is economically attractive because water, the diluent, is inexpensive. Surfactants are used to stabilize the emulsion by preventing the oil droplets from coalescing, thus maintaining low interfacial tension and ensuring the emulsion remains stable during transport. The resulting emulsions often exhibit pseudoplastic or shear-thinning behavior, meaning their viscosity decreases as the shear rate increases. However, the choice and cost of surfactants, as well as the challenges of separating the oil and water phases at the destination, are key limitations of this technique.
Studies have shown that the rheology of O/W emulsions is influenced by factors such as temperature, surfactant concentration, salinity, oil volume fraction, and homogenization conditions. For example, Hoshyargar and Ashrafizadeh (2013) found that optimal conditions for viscosity reduction included a temperature of 25°C, Na2CO3 concentration of 2,000 ppm, NaCl concentration of 5,000 ppm, oil volume fraction of 0.7, and homogenizer revolutions of 22,500. Under these conditions, the viscosity of crude oil was reduced by 90–99%. Hasan et al. (2010) also demonstrated that emulsions prepared with nonionic surfactants (Triton X-100) significantly reduced viscosity, with a 20% reduction for a 10% aqueous solution and a 35% reduction for a 20% solution at 25°C. The emulsions exhibited pseudoplastic behavior at low shear rates but behaved as Newtonian fluids at higher shear rates, where viscosity became independent of temperature and shear rate.
Bitumen, a highly viscous crude oil, can also be effectively transported as an O/W emulsion. At room temperature, the viscosity of bitumen is around 7,000,000 cP, compared to 1 cP for water. Dispersing bitumen in water drastically reduces its viscosity, and like crude oil emulsions, bitumen emulsions show shear-thinning behavior. The viscosity of these emulsions increases with the concentration of the dispersed phase and is highly dependent on shear rate.
Despite the advantages of O/W emulsions, challenges remain. Breaking the emulsion to recover the original hydrocarbon is a complex process, and the choice of surfactant depends on the specific composition of the oil and aqueous phase. Additionally, surfactants are expensive, and economic considerations may limit their use. Overall, while O/W emulsions offer a promising solution for transporting heavy oils, further research is needed to optimize surfactant selection, emulsion stability, and cost-effectiveness (Santos, 2017).
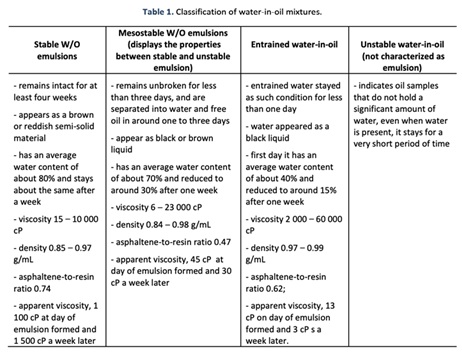
7.5. Economic and Environmental Considerations
The use of diluents in the oil and gas industry plays a crucial role in enabling the transportation of heavy crude oil. However, this practice comes with economic and environmental challenges that impact operational costs, sustainability, and regulatory compliance.
1. Cost Factors
- Supply Chain Costs:
The procurement and transportation of diluents contribute significantly to operational expenses. Diluents such as natural gas condensate, naphtha, and synthetic crude oil need to be sourced from production facilities, transported to blending sites, and then mixed with heavy crude before pipeline transportation. These logistical requirements increase overall costs. - Sourcing Issues:
The availability of diluents varies based on regional supply and market conditions. In some cases, refineries or oil sands operations may face shortages, requiring them to import diluents, which further drives up costs. Dependence on a steady supply of diluents also introduces risks related to geopolitical instability, refinery shutdowns, and production fluctuations. - Price Volatility:
Since most diluents are derived from petroleum products, their prices fluctuate with crude oil markets. Factors such as global demand, production levels, and economic conditions can cause significant price swings. This volatility impacts the profitability of oil sands and heavy crude producers, especially when diluent costs rise disproportionately to crude oil prices.
2. Environmental Impacts
- Emission Concerns:
The extraction, processing, and transportation of diluents contribute to greenhouse gas (GHG) emissions. Since diluents are hydrocarbons, their production involves refining and processing, both of which release CO₂ and other pollutants into the atmosphere. Additionally, when blended with heavy crude, diluents increase the overall volume of hydrocarbons transported, leading to greater emissions during combustion. - Spill Risks:
The use of diluents increases the fluidity of crude oil, making it more likely to spread in the event of a pipeline leak or spill. This presents challenges for spill containment and clean-up efforts, as diluted bitumen (dilbit) behaves differently from conventional crude, potentially causing more severe environmental damage. - Safety Regulations:
Due to the environmental and health risks associated with diluents, governments and regulatory bodies impose strict safety measures on their transportation and use. These regulations include restrictions on emissions, spill prevention protocols, and worker safety standards. Compliance with these regulations can add operational costs but is necessary to ensure environmental and human safety.
3. Future Trends
- Reducing Diluent Dependency:
The industry is exploring ways to minimize reliance on diluents by developing alternative transport solutions. One such approach is partial upgrading, a process that modifies heavy crude at the production site to reduce its viscosity without requiring additional diluents. This can lower costs and improve overall efficiency. - Improving Efficiency:
Advances in pipeline heating technologies, drag-reducing agents (DRA), and emulsification techniques are helping reduce the amount of diluent needed for transport. These innovations enhance flow properties while maintaining pipeline integrity and reducing environmental impact. - Sustainable Solutions:
Research is ongoing into the use of bio-based diluents and recycled hydrocarbon products to replace traditional petroleum-based diluents. For example, studies have shown that hydrocarbons derived from plastic waste can be used to dilute heavy crude oil, providing a dual benefit of reducing plastic pollution and enhancing crude oil transport efficiency.
As the oil and gas industry evolves, balancing economic feasibility with environmental responsibility remains a top priority. Companies are continuously seeking innovative solutions to optimize costs, enhance safety, and reduce the ecological footprint of crude oil transportation.
Conclusion:
In conclusion, the use of diluents in the oil and gas industry is indispensable for the efficient transportation of heavy crude oil and bitumen, which are otherwise too viscous to flow through pipelines. By blending heavy crude with diluents such as natural gas condensate, naphtha, or synthetic crude, the viscosity is significantly reduced, enabling smoother and more cost-effective transport. However, this practice is not without its challenges. The economic costs associated with sourcing, transporting, and blending diluents, coupled with price volatility and supply chain complexities, pose significant operational hurdles. Additionally, the environmental impact of diluent use, including greenhouse gas emissions, spill risks, and regulatory compliance, underscores the need for more sustainable practices.
The industry is actively exploring innovative solutions to mitigate these challenges. Advances in alternative diluents, such as hydrocarbons derived from recycled plastic waste, offer promising avenues for reducing both environmental impact and dependency on traditional petroleum-based diluents. Furthermore, emerging technologies like partial upgrading, pipeline heating, and emulsification are being developed to enhance transport efficiency and reduce the volume of diluents required. As the industry continues to evolve, the focus remains on striking a balance between economic viability and environmental responsibility. By adopting more sustainable and efficient practices, the oil and gas sector can ensure the continued transport of heavy crude oil while minimizing its ecological footprint and operational costs.
References:
[Online] / auth. Dombor. – 2025. – https://www.dombor.com/crude-oil-transport/.
[Online] / auth. cer-rec. – 2022. – https://www.cer-rec.gc.ca/en/data-analysis/energy-markets/market-snapshots/2022/market-snapshot-diluent-growing-share-total-crude-oil-supply.html?utm_source=chatgpt.com.
[Online] / auth. Choksi Himanshu. – 2024. – https://www.sciencedirect.com/science/article/pii/S2096249524000656#bib19.
[Online] / auth. Cuauhtémoc Pozos Vázquez Gerardo Martinez-Narro. – 2019. – https://www.researchgate.net/publication/331887219_Viscosity_reduction_of_heavy_crude_oil_by_dilution_with_hydrocarbons_obtained_via_chemical_recycling_of_plastic_wastes.
[Online] / auth. Mansor. – 2017. – https://www.portalabpg.org.br/bjpg/index.php/bjpg/article/viewFile/575/289.
[Online] / auth. Mansur. – 2017. – https://www.portalabpg.org.br/bjpg/index.php/bjpg/article/viewFile/575/289.
[Online] / auth. Oliveira Santos, Mansur. – 2017. – https://www.portalabpg.org.br/bjpg/index.php/bjpg/article/viewFile/575/289.
[Online] / auth. Oliveria santos, mansur. – 2017. – https://www.portalabpg.org.br/bjpg/index.php/bjpg/article/viewFile/575/289.
[Online] / auth. P. Gateau I. Hénaut. – 2004. – https://www.researchgate.net/publication/245277641_Heavy_Oil_Dilution.
[Online] / auth. Rakesh Kumar Ratnakar a Sivakumar Pandian a , Hepzibah Mary b , Himanshu Choks. – 2024. – https://www.sciencedirect.com/science/article/pii/S2096249524000656#:~:text=This%20technique%20adds%20less%20viscous,flow%20of%20heavy%20crude%20oil..
[Online] / auth. Santos. – 2017. – https://www.portalabpg.org.br/bjpg/index.php/bjpg/article/viewFile/575/289.
[Online] / auth. Santos Oliveria, Mansur. – 2017. – https://www.portalabpg.org.br/bjpg/index.php/bjpg/article/viewFile/575/289.