The Role of Diluent in Bitumen and Heavy Oil Production
1. Introduction
Bitumen and heavy oil play a significant role in global hydrocarbon reserves, particularly as conventional oil resources decline. The increasing demand for energy has driven the need to extract oil from unconventional sources, requiring advanced recovery techniques. One of the primary methods for in-situ bitumen extraction is steam-assisted gravity drainage (SAGD), which is widely used in the industry. However, this technique is highly energy-intensive and has significant environmental and climate-related impacts.
A combination of steam and solvent injection has emerged as a promising method to reduce the energy intensity of in-situ bitumen recovery. Due to its high viscosity, bitumen cannot be produced using conventional oil recovery techniques. The extreme thickness of bitumen presents various challenges in recovery, production, transportation, and refining. Incorporating diluents and organic solvents into bitumen significantly reduces its viscosity, facilitating smoother flow and easier processing.
Several studies have explored the thermos-physical properties of pure solvents and bitumen, providing essential data for the optimization of extraction and transportation processes. However, detailed thermos-physical property data on bitumen-solvent systems remain limited. Further research is essential to accurately model and simulate reservoir behaviour, ultimately improving the design and efficiency of bitumen recovery techniques (Mohammad Shah Faisal Khan, 2024).
2. Role of Diluent in Reducing Viscosity and Enabling Transportation
Bitumen, a highly viscous and dense form of crude oil, presents significant challenges in transportation due to its thick, tar-like consistency. Unlike conventional crude oil, bitumen does not flow naturally under standard conditions, making pipeline transport impractical without modification. One of the most effective methods for overcoming this challenge is diluent blending, which involves mixing bitumen with a lighter hydrocarbon to reduce its viscosity. This process transforms bitumen into a more fluid state, enabling its movement through pipelines to refineries for further processing (Cuauhtémoc Pozos Vázquez, 2019).
3. Mechanism of Diluent Blending
The addition of a diluent is essential to make bitumen pipeline-compatible. A diluent is a light hydrocarbon, typically composed of natural gas condensates, synthetic crude oil, or naphtha. When blended with bitumen, the diluent acts as a solvent, effectively disrupting the strong intermolecular forces that make bitumen highly viscous.
How It Works: The lighter hydrocarbon molecules in the diluent intermingle with the heavier molecules in the bitumen, reducing the overall density and viscosity of the mixture. This process allows bitumen to achieve a lower resistance to flow, making it suitable for pipeline transportation.
Result: The blended product, known as diluted bitumen (dilbit), has a significantly lower viscosity than pure bitumen. Dilbit can flow efficiently through pipelines without requiring excessive energy for pumping, making it a practical solution for long-distance transportation (P. Gateau, 2004).
4. Composition and Types of Diluted Bitumen (Dilbit)
Diluted bitumen, or dilbit, is a mixture of 70–80% bitumen and 20–30% diluent or lighter hydrocarbons. Bitumen, a highly viscous and dense crude oil, requires dilution to make it flow able for transportation through pipelines. The choice of diluent influences the properties of dilbit, and there are four primary classifications based on the type of diluent used.
Standard dilbit consists of bitumen blended with gas condensates, which effectively lowers viscosity, making it easier to transport. Synbit is a combination of bitumen and synthetic crude oil, which improves its refining potential but may still require additional processing. Lightened dilbit includes gas condensates with added C4 and C5 hydrocarbons, making the mixture lighter and slightly more volatile. Another variation is dilbit blended with synthetic naphtha, which further enhances flow properties but has different refining characteristics.
A modified version known as dilsynbit is a combination of synthetic crude and condensates mixed with bitumen. While it shares similarities with synbit, it is not classified as a separate category but serves as an intermediate product with properties that vary depending on the specific blend (Apps, 2021).
4.1. Chemical Composition of Dilbit
Dilbit contains a range of volatile organic compounds (VOCs) and hydrocarbon components that influence its behaviour and environmental impact. One of the key components is BTEX (Benzene, Toluene, Ethylbenzene, and Xylene), which typically makes up 0.8–1.2% of dilbit by volume. These compounds are highly volatile and evaporate quickly when exposed to air, contributing to air pollution and potential health hazards.
Another significant group of compounds present in dilbit is polycyclic aromatic hydrocarbons (PAHs), which are persistent in the environment and can have long-term ecological effects. Additionally, dilbit contains alkanes and petroleum biomarkers, including hopanes, terpanes, and steranes, which help determine the source and characteristics of the oil. These biomarkers are used in forensic analysis to trace oil spills and assess the impact of bitumen products in the environment (Apps, 2021).
4.2. Behaviour of Dilbit Upon Release
When dilbit is exposed to the atmosphere, its lighter components evaporate, leaving behind a heavier, more viscous bitumen residue. This evaporation process occurs rapidly, particularly for BTEX compounds, which dissipate within hours to days. As the light hydrocarbons are lost, the remaining bitumen becomes denser and stickier, making clean-up efforts more challenging in the event of a spill.
The properties of the residual bitumen vary based on the original bitumen type and diluent composition, leading to highly variable behaviour. In some cases, the remaining bitumen may float on water, while in others, it can sink depending on the surrounding environmental conditions and interactions with sediments. This variability complicates spill response strategies and requires tailored approaches for different types of dilbit products.
Understanding the composition and behaviour of dilbit is essential for efficient transportation, refining, and environmental management. The selection of diluent, the blending process, and the handling of dilbit all play a crucial role in ensuring the safe and effective movement of bitumen through pipelines while minimizing environmental risks (apps.dtic, 2021).
5. Comparison of Physical and Chemical Properties of Different Dilbit Blends
The tables below provide a summary of the physical and chemical properties of various diluted bitumen (dilbit) products, classified based on the type of diluent used in their composition. The key properties listed include density (kg/m³), sediment content (ppmw), light ends (vol%), and BTEX (vol%), which influence the behaviour of these products during transportation and refining.
Standard Dilbit (Gas Condensates)
Standard dilbit consists of bitumen mixed with gas condensates, which help lower viscosity for easier pipeline transportation. The table lists four standard dilbit blends:
- These products have densities ranging from 918 to 933 kg/m³, making them among the least dense dilbit types.
- The sediment content varies, with WCS having the highest sediment levels (261–307 ppmw), which may affect refining efficiency.
- Light ends (volatile components that evaporate easily) are highest in AWB (22–26%) and lowest in WCS (17–20%).
- BTEX (Benzene, Toluene, Ethylbenzene, Xylene) content is relatively high, with AWB having the most (1.1–1.4%)and WCS the least (0.7–1.0%), indicating differences in volatility and potential environmental impact.
Synbit (Synthetic Crude)
Synbit is a mixture of bitumen and synthetic crude oil, making it different from standard dilbit in refining characteristics. The listed blends are:
- Statoil Cheecham Blend (SCB), Long Lake Heavy (PSH), Statoil Cheecham Synbit (SCS), Surmont Heavy Blend (SHB), and Suncor Synthetic H (OSH).
- These blends generally have higher densities (924–940 kg/m³), making them heavier than standard dilbit.
- Sediment content is variable, with SCB having a wide range (70–268 ppmw) and OSH having the lowest (39 ppmw).
- Light ends content is lower compared to standard dilbit, ranging from 22–26% in SCB to only 9–11% in OSH, meaning they are less volatile.
- BTEX levels are lower in synbit (mostly 0.4–1.2%), reducing its potential for rapid evaporation and air pollution compared to standard dilbit.
Lightened Dilbit (Gas Condensates with Added C4/C5 Hydrocarbons)
Lightened dilbit uses gas condensates with added short-chain hydrocarbons (C4 and C5) to further modify viscosity and volatility. The Peace River Heavy (PH) blend is listed under this category.
- Density (926–935 kg/m³) is comparable to synbit.
- Sediment content (67–127 ppmw) is moderate.
- Light ends content (21–24%) is similar to standard dilbit, making it more volatile than synbit.
- BTEX content (0.9–1.1%) is comparable to standard dilbit, meaning it has similar environmental considerations.
Dilbit with Synthetic Naphtha
This category includes bitumen blended with synthetic naphtha, which provides different refining characteristics compared to condensate-based diluents. The table lists three blends:
- Borealis Heavy Blend (BHB), DilSynbit (a modified synbit with condensates), and Albian Heavy Synthetic (AHS).
- Densities vary, with BHB at 922–933 kg/m³ and AHS at 935–942 kg/m³, making AHS one of the heaviest blends listed.
- Sediment levels are highest in AHS (555–1018 ppmw), which may pose refining challenges.
- Light ends content (22–26%) is comparable to standard dilbit.
- BTEX levels (0.8–1.1%) are within the range of other dilbit types, indicating moderate volatility.
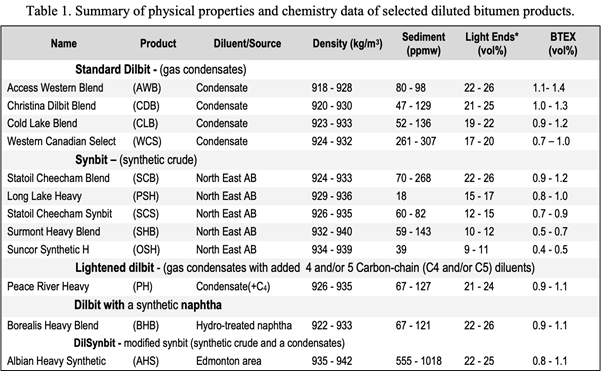

The table 2 compares the physical properties of different oil types, including gasoline, diesel, light crude, diluted bitumen (dilbit), and heavy crude. The properties listed include density, API gravity, viscosity, flash-point, solubility in water, pour-point, and interfacial tension.
- Density increases from gasoline (720 kg/m³) to heavy crude (880–1000 kg/m³), with dilbit falling between 824–941 kg/m³.
- API Gravity, which measures how light or heavy the oil is compared to water, decreases from gasoline (65°) to heavy crude (10–30°), with dilbit ranging from 18–39°.
- Viscosity, indicating resistance to flow, is extremely high for heavy crude (up to 50,000 mPa.s), while dilbit varies widely (270.5–265,263 mPa.s).
- Flash-point, the temperature at which the oil ignites, varies significantly. Gasoline has the lowest (-35°C), while dilbit can be below -35°C or as high as 58°C.
- Solubility in Water is highest for gasoline (200 ppm) and lowest for heavy crude (5–30 ppm).
- Pour-point, the lowest temperature at which the oil remains fluid, varies from -40°C to 30°C, with dilbit ranging from -30°C to -15°C.
- Interfacial Tension, affecting oil spreading and emulsification, is highest for dilbit (27–150 mN/m), suggesting differences in stability and behaviour compared to other oil types.
6. Review on Diluted Bitumen (Dilbit)
Over the past three decades, extensive research has been conducted on diluted bitumen (dilbit), focusing on its behaviour in various environmental conditions, particularly in salt and fresh water. These studies have examined oil weathering, containment and recovery techniques, and the chemical composition of dilbit in different aquatic settings. The findings contribute to a better understanding of dilbit spills and their implications for environmental management (apps.dtic.mil, 2021).
6.1. Physical Weathering in Salt Water
Studies have investigated the effects of evaporation on different types of dilbit, such as Access Western Blend (AWB) and Cold Lake Blend (CLB), compared to intermediate fuel oils. Research found that both types of dilbit initially float on salt water when free of sediment, even after undergoing evaporation. However, as evaporation progresses, the density, viscosity, and pour-point of dilbit increase, leading to a potential change in its behavior. Some studies demonstrated that dilbit could sink under specific natural weathering conditions after several days. Factors such as wave action, sunlight, wind, and salinity influence the rate at which dilbit weathers and its potential for submergence. Additionally, temperature and seasonal variations affect the rate of photolytic degradation of hydrocarbons in dilbit, with higher solar intensity leading to increased chemical transformation.
6.2. Chemical Weathering in Salt Water
Research measuring the concentrations of benzene, toluene, ethylbenzene, and xylenes (BTEX) and polycyclic aromatic hydrocarbons (PAHs) in dilbit showed that the presence of condensates in dilbit formulations influenced the levels of these toxic compounds in the water. Studies found that cooler temperatures during certain seasons resulted in higher concentrations of these compounds, which could have environmental and ecological consequences. Another key finding was that the breakdown of petroleum hydrocarbons occurred at different rates depending on environmental conditions, with aromatic hydrocarbons and alkanes showing faster photo-oxidation, while biomarkers such as steranes and terpanes exhibited slower degradation rates.
6.3. Containment and Recovery in Salt Water
Research has tested various oil containment and diversion techniques for spilled oil, including river booms, mesh nets, and bubble nets. Results indicated that the effectiveness of these tools decreased as water velocity increased. Additionally, studies evaluated the use of skimmers and other recovery devices, noting that standard oil spill response equipment could be effective in the early stages of a dilbit spill while the oil remains on the surface. However, as dilbit weathers and becomes more viscous, recovery efforts may require more powerful pumps and specialized equipment.
6.4. Physical Weathering in Fresh Water
Studies on dilbit in fresh water environments have examined the impact of photo-oxidation and natural weathering on the oil’s density and buoyancy. Research showed that dilbit could remain buoyant for several days but could eventually sink as it undergoes evaporation and absorbs water. In controlled experiments, dilbit exposed to ultraviolet (UV) light formed oil droplets due to chemical breakdown, affecting its dispersion in water. Other studies found that weathered dilbit could increase in density over time, leading to sinking under specific conditions, particularly in low-energy environments with minimal water movement.
6.5. Chemical Weathering in Fresh Water
Studies analysing the behaviour of polycyclic aromatic compounds (PACs) in fresh water found that concentrations of certain toxic compounds increased during the initial phases of a spill but later began to decline. Researchers measured levels of phenanthrenes, dibenzothiophenes, and fluorenes in water samples and observed a rise in concentrations for the first few days, followed by a gradual decrease. This behaviour suggests that environmental factors such as microbial degradation and water movement play a role in the dissipation of these toxic compounds over time.
6.6. Containment and Recovery in Fresh Water
Experiments on containment and recovery strategies for dilbit in fresh water environments have evaluated different techniques for oil spill response. Tests on river booms, mesh nets, and bubble nets showed that their efficiency decreased as water velocity increased. Studies also examined the recovery of dilbit in fresh water compared to traditional heavy oil spills in salt water. Findings indicated that standard skimmers could effectively recover dilbit while it remained on the surface. However, as dilbit becomes more viscous over time, recovery operations may require more powerful pumps and specialized containment strategies.
7. Extraction Methods: Oil Sands and Ultra-Heavy Crude Production
Bitumen is primarily extracted from oil sands, with Canada and Venezuela being the largest producers. Due to its highly viscous nature, bitumen does not flow naturally and must be extracted using specialized techniques. There are two main methods for bitumen extraction: surface mining and in-situ extraction (apps.dtic, 2021).
7.1. Surface Mining
Surface mining is used when bitumen deposits are close to the surface. In this process, large volumes of bitumen-rich sand are excavated and transported to processing facilities, where hot water is used to separate the oil from sand and clay. This method is effective for shallow reserves but has significant environmental impacts, including land disturbance and water usage.
7.2. In-Situ Extraction
For deeper deposits, in-situ extraction is the preferred method. One of the most commonly used in-situ techniques is Steam-Assisted Gravity Drainage (SAGD), which involves injecting steam into the reservoir through horizontal wells. The heat lowers the viscosity of the bitumen, allowing it to flow to production wells, where it is pumped to the surface. In-situ extraction is less disruptive to the landscape than surface mining, but it requires large amounts of energy to generate steam, making it more carbon-intensive.
7.3. Ultra-Heavy Crude Recovery
Ultra-heavy crude oil, which has an extremely high viscosity, is found in reservoirs where natural flow is nearly impossible. This type of crude requires enhanced oil recovery (EOR) techniques to improve mobility and facilitate extraction. Steam flooding, a common EOR method, involves injecting high-pressure steam into the reservoir to reduce viscosity and enhance oil flow. Another technique, solvent-assisted recovery, uses chemical solvents to dilute the heavy crude, making it easier to extract. These methods allow for the production of ultra-heavy crude that would otherwise remain trapped in the reservoir.
Once extracted, both bitumen and ultra-heavy crude present significant transportation challenges due to their high viscosity and resistance to flow. To facilitate pipeline transport, producers must mix the extracted oil with diluents such as natural gas condensates or lighter crude oils. This blending process reduces viscosity, enabling efficient movement through pipelines. Without the addition of diluents, bitumen and ultra-heavy crude would require expensive heating or alternative transportation methods such as rail or trucking, which can increase costs and logistical complexity.
8. Types of Diluents Used in the Oil Industry
Several types of diluents are used depending on the source and requirements of the oil production process:
1. Natural Gas Condensates (C5-C12 hydrocarbons)
- A mixture of pentanes (C5), hexanes (C6), and heavier hydrocarbons, often sourced from natural gas fields.
- One of the most common diluents for Canadian Oil Sands production.
- It has a high blending compatibility with bitumen.
2. Naphtha (Light Hydrocarbon Blend)
- Derived from crude oil refining.
- Provides excellent dilution but may require additional refining before reuse.
- More volatile than condensate, making it useful in specific blending applications.
3. Synthetic Crude Oil (Upgraded Bitumen)
- Partially refined from bitumen to create a lighter, more transportable product.
- Reduces the need for external diluent but requires expensive upgrading facilities.
4. Refined Petroleum Products (Diesel, Kerosene, etc.)
- Occasionally used as diluents in specific operations where other sources are limited.
- Diesel-based dilution can help enhance combustion properties in certain fuel applications.
9. How Diluent Impacting the Oil Industry?
1. Pipeline Infrastructure & Logistics
Using diluent allows bitumen and heavy oil to be transported via conventional pipeline systems, rather than costly rail or truck transport. However, the need for diluent also means:
- Additional processing facilities for diluent recovery.
- Higher transportation costs due to increased volume (diluted bitumen takes up more space than undiluted bitumen).
2. Economics of Diluent Use
Diluent is an added cost in heavy oil production. Some challenges include:
- Supply constraints: Not all regions have access to cheap diluent sources.
- Price volatility: Market fluctuations in natural gas condensate prices impact operating costs.
- Recycling and recovery: Some operations invest in diluent recovery units (DRUs) to minimize long-term costs.
3. Refinery Compatibility
Refineries process diluted bitumen differently than conventional crude.
- Some refineries prefer synthetic crude (SCO) over diluted bitumen due to processing challenges.
- High sulphur and heavy metal content in bitumen requires specialized refining equipment.
10. How Diluent is Recovered and Reused?
Diluent is an essential component in transporting and processing heavy oil and bitumen, but its use comes with economic and logistical challenges. Since diluent increases transportation costs and affects refining efficiency, the recovery and reuse of diluent is a critical part of optimizing operations (Jan Hupka, 2008).
10.1. Separation of Diluent at Refineries and Processing Facilities
Once diluted bitumen (dilbit) or diluted heavy oil reaches its destination—whether a refinery or an upgrading facility—the diluent must be separated before refining or upgrading the oil. The separation process typically occurs in the front-end distillation unit of a refinery, where lighter hydrocarbons, such as condensates and naphtha, are vaporized and collected for reuse (Hupka, 2004).
10.2. Key Steps in Diluent Separation
The separation process begins with heating and flash distillation. The incoming dilbit is heated in a distillation column, causing the lighter hydrocarbons to vaporize while the heavier oil components remain. The vaporized diluent is then condensed and collected separately. In addition to this process, fractional distillation is often used to separate different diluent components, such as C5-C12 hydrocarbons, to enhance quality and reuse potential.
After separation, the recovered diluent is stored in dedicated tanks before being reused in oil sands operations or sold in the market. The recovered diluent is either sent back to upstream operations via pipelines, blended into other crude oils for specific refining needs, or sold as a petrochemical feedstock used in gasoline or solvents (Miller, 2004).
10.3. Methods of Diluent Recovery and Recycling
The efficiency of diluent recovery depends on the type of processing facility and the technology employed. Various methods have been developed to optimize the process.
Diluent recovery units, or DRUs, are commonly installed at oil sands processing plants and refineries. These specialized units recover between 60 and 90 percent of the diluent from diluted bitumen. The recovered diluent is then recycled directly into upstream operations, reducing the need for new diluent purchases.
Flash distillation and solvent extraction is another method used for recovery. This technique involves low-pressure and heat treatment to separate volatile diluent components. It is a more advanced process than basic distillation and allows for higher recovery rates with lower energy consumption.
Membrane-based separation is a newer technology that uses selective membranes to filter and separate diluent from bitumen. This process improves efficiency and reduces energy costs compared to traditional distillation methods.
Gas-assisted diluent recovery is an emerging technique where natural gas is injected into the system to help strip diluent from bitumen. Although this method is still being researched, it shows potential in reducing energy consumption.
Supercritical fluid extraction is another innovative approach that uses supercritical CO₂ or light hydrocarbons to separate diluent without excessive heat. This technique helps recover more diluent while lowering energy inputs, making it a promising solution for the future (King, 2020).
10.4. Efficiency Improvements in Diluent Management
The primary goal of diluent recovery and reuse is to reduce costs, minimize environmental impact, and enhance operational efficiency. Several advancements and strategies have emerged to optimize diluent use.
Increasing diluent recovery rates is one of the most significant improvements in the industry. Advanced fractionation columns and DRUs now allow for up to 90 percent recovery of diluent, significantly reducing the need for fresh supply. Some new technologies are aiming to push this recovery rate beyond 95 percent.
The use of alternative viscosity reduction methods has also contributed to efficiency improvements. Partial upgrading is a pre-processing technique that reduces bitumen viscosity without requiring diluent. Another approach is emulsion-based transport, where bitumen is mixed with water and surfactants instead of using diluent. These alternatives can reduce reliance on diluent while maintaining the fluidity needed for transportation.
Pipeline optimization and diluent return systems have become an essential part of the industry’s efforts to improve efficiency. Some pipeline systems now include dedicated diluent return lines, which allow recovered diluent to be transported back to oil sands sites more efficiently. Companies are also developing closed-loop diluent systems designed to minimize waste.
Digital monitoring and AI-based optimization are playing an increasing role in improving diluent management. Refineries and processing plants use artificial intelligence and machine learning to monitor diluent usage and recovery rates in real-time. This data-driven approach optimizes separation temperatures, pressures, and flow rates to maximize diluent recovery and minimize losses.
Environmental and regulatory considerations are also driving improvements in diluent management. Governments are enforcing lower diluent-to-bitumen ratios (DBR) to reduce overall diluent demand. By improving recovery processes, the industry can lower greenhouse gas emissions associated with diluent production and transportation (Drelich, 2004).
Conclusion
Diluents are essential for reducing the viscosity of bitumen and heavy oil, enabling their transportation through pipelines via diluted bitumen (dilbit). By blending bitumen with light hydrocarbons like natural gas condensates or naphtha, the industry overcomes the challenges posed by bitumen’s high viscosity. The efficiency of this process depends on the type of diluent, blending ratio, and temperature, while environmental concerns, such as VOC emissions and spill risks, require careful management.
Recovery and reuse of diluents through advanced technologies like diluent recovery units (DRUs) and flash distillation improve sustainability and reduce costs. However, economic challenges, such as price volatility and supply constraints, alongside environmental impacts, highlight the need for continued innovation. As global energy demand grows, optimizing diluent use and exploring alternatives will be crucial for sustainable bitumen production.
References:
[Online] / auth. Apps. – 2021. – https://apps.dtic.mil/sti/pdfs/AD1159332.pdf.
[Online] / auth. apps.dtic. – 2021. – https://apps.dtic.mil/sti/pdfs/AD1159332.pdf.
[Online] / auth. apps.dtic.mil. – 2021. – https://apps.dtic.mil/sti/pdfs/AD1159332.pdf.
[Online] / auth. apps.dtic. – 2021. – https://apps.dtic.mil/sti/pdfs/AD1159332.pdf.
[Online] / auth. Apps. – 2021. – https://apps.dtic.mil/sti/pdfs/AD1159332.pdf.
[Online] / auth. Cuauhtémoc Pozos Vázquez Gerardo Martinez-Narro. – 2019. – https://www.researchgate.net/publication/331887219_Viscosity_reduction_of_heavy_crude_oil_by_dilution_with_hydrocarbons_obtained_via_chemical_recycling_of_plastic_wastes.
[Online] / auth. Drelich Jaroslaw. – 2004. – https://www.researchgate.net/publication/268278417_Water-based_bitumen_recovery_from_diluent-conditioned_oil_sands.
[Online] / auth. Hupka Jan. – 2004. – https://www.researchgate.net/publication/268278417_Water-based_bitumen_recovery_from_diluent-conditioned_oil_sands.
[Online] / auth. Jan Hupka Jan D. Miller, Jaroslaw Drelic. – 2008. – https://onlinelibrary.wiley.com/doi/abs/10.1002/cjce.5450820513.
[Online] / auth. King Martin. – 2020. – https://rbnenergy.com/closer-to-home-a-novel-effort-to-recover-diluent-for-reuse-in-albertas-oil-sands.
[Online] / auth. Miller Jan D. – 2004. – https://www.researchgate.net/publication/268278417_Water-based_bitumen_recovery_from_diluent-conditioned_oil_sands.
[Online] / auth. Mohammad Shah Faisal Khan Hassan Hassanzadeh. – 2024. – https://www.sciencedirect.com/science/article/abs/pii/S0016236123022913.
[Online] / auth. P. Gateau I. Henaut. – 2004. – https://www.researchgate.net/publication/245277641_Heavy_Oil_Dilution.